Designing the new Robot - Sealing Elements
- UFRJ Nautilus
- May 28, 2020
- 3 min read
Updated: May 7, 2021
The preparation and eventual construction of a new AUV requires knowledge in different areas of study that together will allow the development of an efficient project. One part of this development process refers to the tightness of the robot. Tightness is nothing more than a term to designate that a certain project is free of spaces such as holes, cracks or porosities that allow it to be filled by some fluid.
As a characteristic, our AUV needs a constant exchange of information that is carried out by cables between elements, such as our propellers, which do not present problems when being in constant contact with water. However, there are elements that cannot receive any drops of water, such as the electronic components in the Main Hull. All this communication between parties, as well as the specific characteristics regarding the possibility of getting wet, make the guarantee of tightness by means of sealing elements extremely important.
Due to our Know-How as a competition team that creates AUVs, we have the ability to better choose sealing elements, either due to their shape or function. For this, we first define what should be considered when choosing a sealing element:
Temperature: Normally high or very low temperatures make sealing difficult, since the sealing element will be exposed to critical temperatures, which will cause changes in the expansion of the element or mechanical problems in it.
Finishing the parts: To ensure that the calculations made when choosing the sealing element are correct and do not happen unforeseen events.
Pressure: Higher fluid pressures make sealing more difficult, as it increases the likelihood of leakage into the watertight area.
Physical State: Most liquid and gaseous fluids are more common to be sealed, the first being much easier to be sealed due to physical characteristics than the second.
There are two classifications of sealing elements: the fixed joints that can be found in pipes and reservoirs, and the movable joints in objects that require rotation and translation movements.
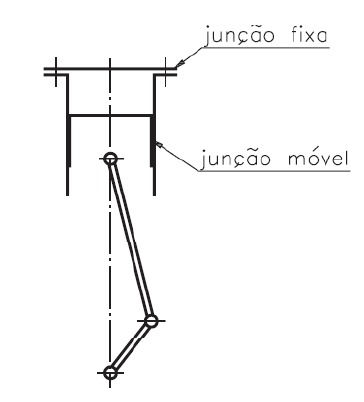
The sealing at the fixed joints can be done directly or by intermediate elements called fittings, which are flexible parts placed between two rigid surfaces. To ensure tightness in the Main Hull and in the attachments of our AUV, we chose to use the joint with a trim element, the o-rings.
The O-Ring is a toroidal object, also known as the O-Ring seal ring, made of elastomer, plastic or metal that aims to prevent the passage of fluids from one medium to another.
Placed inside the cover in cavities specifically produced to receive them and being in contact with the two parts to be sealed, the pressure produced between these parts shapes the o-ring, making the seal. That is why the choice of the ring is made, we must then take into account the area and the fluid that will be sealed, in addition to considering the deformation that the o-ring needs to have to guarantee the sealing.
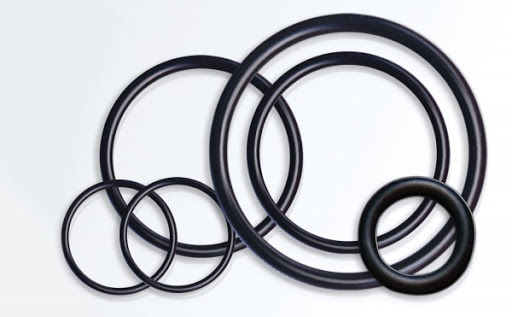
Although the use of the o-ring is a simple and economical solution for sealing the hull, it is not the solution for all the problems, since the material wears out after a certain time (which leads us to change them periodically), along with the fact that there are some limitations of use, such as high temperatures.
Another point that we need to pay attention to is the metal cover of the main hull. So that there is no fluid passing through the thread of the submarine connectors, liquid thread sealant is used. The choice of the liquid product is given by the easy application, full filling of any space where there can be fluid exchange between the media and the possibility of withdrawal and reapplication.
Innovation
As we have seen, the sealing methods are diverse and each is better for different sealing situations. For our new robot, we seek to improve every element more and more, and the sealing part would be no different. In addition to the methods already used today, we seek solutions to new problems and improvements that may arise. One of the methods found was sealing by flanges.

Flange sealing is efficient for sealing rugged or rough surfaces and they can be made of different materials, such as aluminum, nylon, rubber, among others.
The flanged joint consists of two flanges, a sealing washer and screws whose quantity depends on the material's characteristics. The tightness is ensured by the axial compression of the sealing washer (in which its material is important) and by tightening the screws. Its main characteristics are the precision of assembly and the possibility of assembly and disassembly of the sealed line.
This new possibility of sealing reinforces once again the team's ability to be in a continuous process of innovation in search of the best representation in Robonation.
Written by Giulia Carvalho and Pedro Gomes
Commenti